Hollow glass microsphere is a kind of hollow, thin-walled, high-strength, smooth surface micro sphere, which is a new micro scale lightweight inorganic material developed in the 1950s and 1960s. In addition to the advantages of low density, high strength, low heat conduction, high wave transmission and good stability, it also has excellent properties that other non-metallic mechanical materials do not have, such as insulation, self-lubricating, sound insulation, fire resistance, corrosion resistance and radiation protection. Therefore, it is widely used, even indispensable in some special fields.
In the early years, it was found that some by-products of fly ash were pearl like hollow microspheres with a diameter of 20~200 under the microscope μ The shell thickness varies from 5% to 30% of the diameter, and its main components are SiO2, Al2O3, CaO, MgO, Na2O, K2O, etc. This kind of sphere has small specific gravity, high surface pressure, strong wear resistance, good flame retardancy, good acid resistance and high temperature resistance, so it has been exploited for new functions. At the early stage of the development of artificial hollow glass beads, due to the high cost, they were mainly used in cutting-edge fields such as aerospace and national defense. Later, the United States and Japan took the lead in the research and development and mass production of hollow glass beads, which formed a situation where hollow glass beads were monopolized by foreign countries and became one of the neck materials in China.
With the development of science and technology in China, hollow glass beads can be industrialized in China, and gradually become a new functional material with relatively low price and rich functions, which has been widely used in military and civilian fields such as thermal insulation materials, insulation materials, composite materials, petrochemical, coatings, rubber, etc.
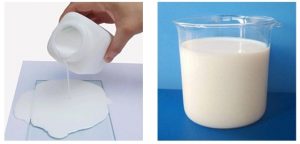
When visiting the application exhibition hall of Shenglaite, the technicians introduced to the small group that Shenglaite’s hollow glass beads have been successfully applied in more than 20 downstream fields, including daily consumer goods, industrial supplies and cutting-edge aerospace fields.
In terms of 5G communication, hollow glass beads can help improve the transmission rate because their hollow glass material has a low dielectric constant of 1.0~2.0. At present, downstream applications involved include 5G base station and radome materials, 5G mobile phone middle frame and backplane, Internet of Things equipment, etc.
In terms of lightweight of rubber, elastomer and vehicles, hollow glass beads have a good role in reducing the specific gravity, which can reduce the weight of rubber and plastic composites by 8%~10%. In addition, hollow glass beads can also effectively improve the processing performance of materials, increase rigidity and resilience, and improve a series of special functions of materials, such as heat insulation, sound insulation and noise reduction, and flame retardancy. They are widely used in shoes, flexible pillows, car shells, special parts and other products.
In the coating industry, the characteristics of hollow glass microspheres, such as micron particle size, microsphere effect and hollowness, endow the coating with better heat insulation and heat preservation effect, and create a new cooling coating integrating reflection, radiation and efficient heat insulation. It is not only used in military and aerospace equipment, but also widely used in oil pipelines, oil storage tanks, communication base stations, large grain storage silos and other industries.
As an anti-corrosion coating, the addition of hollow microspheres makes the product have better antifouling, anti-corrosion, anti ultraviolet, anti yellowing, and scratch resistance effects, which can be widely used in weather resistant sunscreen and thermal insulation outdoor coatings, automotive coatings, ship antifouling coatings, anti-corrosion coatings, etc.
In the adhesive industry, the addition of hollow microspheres can reduce the density of the adhesive, reduce the volume cost, improve the rheological property of the adhesive, improve the thixotropy and chemical corrosion resistance, and give the product better sound insulation, heat insulation, low heat conduction and dielectric properties, as well as better anti warping and anti cracking properties. Hollow glass beads are widely used in adhesives such as silicone, epoxy resin, acrylic acid, polyurethane, synthetic rubber, etc. In addition to the above, hollow glass beads have a very typical application for oilfield cementing, which is also the field with the largest consumption for a long time. The use of oilfield cementing includes low-density drilling fluid and cementing cement.
The low-density drilling fluid added with hollow glass beads not only has higher chemical stability and excellent fluidity, but also has better lubrication effect. It can reduce friction during drilling, extend the service life of drill pipe, drill bit and other equipment, and greatly improve the drilling speed and operating efficiency. The addition of hollow glass beads in cementing cement gives the product the characteristics of low density, high strength and easy flow. It is one of the main ways to solve the problem of low leakage and low return of cement slurry in low pressure and leaky wells. It can effectively control the water loss rate and prevent pollution. The 24h compressive strength can reach more than 15MPa, and can improve the cementing quality and extend the life of oil wells.
ARTICLE SOURCE: Powder ring network