Composites that simultaneously combine light weight with high electrical and low thermal conductivity are very desirable for aerospace, marine, and energy applications but are hard to achieve in practice. Now researchers think they may have the answer in the form of hollow glass microspheres covered with carbon nanofibers, which can be used as a filler for polymer composites.
Hollow glass microspheres are well-known additives for polymer composites because of their light weight and low thermal conductivity. But the lack of interaction between glass microspheres and the polymer matrix reduces the composite’s strength. Carbon nanotubes and fibers hold promise as fillers for polymer composites because of their electrical conductivity. To get just the right balance of properties, the researchers sought to bring together the best attributes of each of these fillers in one material.
By growing carbon nanofibers directly on the surface of hollow glass microspheres, we do not need complicated techniques to disperse the nanofibers in the matrix so we can mix them as a standard microfiller.
This article comes from materialstoday edit released
Posted by admin on September 8, 2020 at 5:39 am under Hollow Glass Microspheres.
Comments Off on Hollow glass microspheres combines novel properties.
Plastisols are relatively stable fluid dispersions of finely divided plastic resin particles in a liquid plasticizer with a small amount of diluent (solvent).
Further additives are introduced to the plastisols, such as fillers, pigments, adhesion promoters, rheology auxiliaries (separation inhibitors), heat stabilizers, blowing agents, reactive (capable of cross-linking) additives, and water-absorbing substances (calcium oxide).
Hollow glass microsphere fillers are mainly used to reduce density while also providing viscosity control, sag, and impart thixotropy to the unfluxed plastisol solution increasing shelf life of low density seam sealers. Plastisol based automobile coatings and seam sealers must meet rigid standards set by various automobile manufacturing companies. A very important requirement for plastisol coatings is that they be lightweight.
As plastisol manufacturers strive for lighter and hence more fuel efficient vehicles, hollow glass microspheres has become a crucial part of the plastisol formulations as key raw material filler. Hollow glass microspheres in plastisols are described in detail in this chapter.
This article comes from sciencedirect edit released
Posted by admin on September 1, 2020 at 7:56 am under Hollow Glass Microspheres.
Comments Off on Hollow Glass Microspheres in Plastisols.
Traditional Applications for Hollow Glass Microspheres
- Low density fillers for composites with polymers and concrete
- Thermally insulating paint
- Thermally insulating tapes
- Syntactic foams for submersibles
- Targets for laser fusion systems (D/T filled)
Modern Applications for Hydrogen-Filled Hollow Glass Microspheres
- Hydrogen storage
- Hydrogen separation and purification
- Radiation shielding for manned space flight
Summary
- Hollow glass microspheres have many attractive features as a hydrogen storage medium
- Optically-induced outgassing of hydrogen from glass is significantly faster than conventional heating
- Current work seeks to demonstrate feasibility using hollow glass microspheres
This article comes from lehigh edit released
Posted by admin on August 25, 2020 at 7:12 am under Hollow Glass Microspheres.
Comments Off on Novel Applications of Hollow Glass Microspheres.
Hollow glass microspheres are available as commercial products in large quantities at cost of less than US$2 per kilogram, which would be expected to decrease with economies of scale.
The raw materials are relatively inexpensive, the production processes are well established, and the durability of the spheres is such that they can withstand a large number of filling/outgassing cycles. The materials can easily be recycled to produce new spheres to replace those broken during service.
As a result, hollow glass microspheres appear to be the cheapest of all current materials for the solid-state storage of hydrogen.
This article comes from sciencedirect edit released
Posted by admin on August 18, 2020 at 6:45 am under Hollow Glass Microspheres.
Comments Off on FUELS – Hollow Glass Microspheres.
The production of hollow glass microspheres is part of an ongoing research and development program started in 1974. And aimed at developing a method for mass producing glass fuel containers for use in inertial confinement fusion (ICF) experiments. Several previous reports have described the development of the liquiddroplet technique for the production of hollow glass microspheres.
In this paper, ive review previous data along with tie results from our more recent studies to present a detailed picture of the preparation method and properties of the hollow glass microspheres. The production of the high-quality hollow glass microspheres needed for laser fusion targets requires us to optimize a number of processing parameters.
In the past, we used a largely empirical approach to determine the proper operating conditions. Although this approach was successful, it was also time consuming and manpower intensive. To help guide and interpret our present experimental work, we have developed a simple, onedimensional (1-D) model to simulate the sphere formation process.
The model has been used to quantify the effects of several key process variables such as the column temperature profile, purge-^as composition, droplet size and composition, and glass film properties.
This article comes from osti edit released
Posted by admin on August 11, 2020 at 9:13 am under Hollow Glass Microspheres.
Comments Off on Properties of Hollow Glass Microspheres.
Imagine lighter-weight vehicles that can travel farther on less fuel. More efficient ways to drill for oil and insulate deepsea pipelines. Paint that helps keep homes cooler on hot, sunny days. In all these ways and more, hollow glass microspheres are helping a wide range of industrial sectors solve design challenges and reach new levels of performance and productivity.
Hollow glass microspheres are high-strength, low-density hollow glass microspheres made from soda-lime borosilicate glass. They are nonporous, chemically stable and provide excellent water and oil resistance.
Strong enough to survive processing, they can be incorporated into a wide range of polymers for density reduction. And the benefits of hollow glass microspheres go far beyond lightweighting: the inherent properties of these microspheres provide a number of unique performance and processing advantages.
Posted by admin on August 4, 2020 at 8:42 am under Hollow Glass Microspheres.
Comments Off on Hollow glass microspheres for Industrial.
Hollow glass microspheres products offer formulators flexibility in polymer composites. The addition of hollow glass microspheres to fiberglass reinforced plastics (FRP), epoxy, compounds, and urethane castings can provide weight reduction cost savings and improved impact resistance. Insulating features of hollow glass microspheres also work to the chemists’ advantage in thermal shock and heat transfer areas. Sphere One’s hollow glass microspheres are your best choice when you need lightweight filler.
A range of products with densities from 0.14 to 0.80 g/cm3 provides choices to best fit mixing and target weight requirements.
When used in polymer concrete, hollow glass microspheres provide a cost effective alternative without degrading physical properties.
Hollow glass microspheres are used to enhance performance and reduce viscosity in paints and coatings and as lightweight additives in plastic parts. They are chemically inert, non-porous, and have very low oil absorption.
Applications:
Adhesives, Auto Body Filler, Caulk, Coatings, Cultured Marble, Epoxy, Putty, Sealants.
Posted by admin on July 28, 2020 at 8:20 am under Hollow Glass Microspheres.
Comments Off on Precision Hollow Glass Microspheres.
Syntactic foams (SF) with robust impermeable hollow glass microspheres as density adjuster have drawn much attention because of their easy-tailored low density, high mechanical strength and excellent performance especially when used in high pressure aqueous environment.
In this work, specially fabricated hollow glass microspheres with high strength to weight ratio were employed for the controlled fabrication of high strength lightweight syntactic foams. Special attention has been paid on the effects of surface physicochemical status modification of the HSMs on the mechanical strength and mechanical performance evolution in various external environments. It is found that the surface physicochemical status modification of the hollow glass microspheres contributes more on the enhancement of the fracture toughness compared with that of the compressive strength.
Moreover, compared with those of the pristine SF, the mechanical strength of the SF samples after different environmental exposure display a more remarkable improvement due to the surface physicochemical status modification of the HSMs, indicating an enhanced environmental stability. This work provides an additional insight to the mechanical strength and aging resistance control of SF, which holds the potential to be extended to the property improvement of similar composites with various types of silicate or glass fillers.
This article comes from sciencedirect edit released
Posted by admin on July 14, 2020 at 9:00 am under Hollow Glass Microspheres.
Comments Off on Effects of hollow glass microsphere surface property on the mechanical performance of high strength syntactic foams.
Hollow Glass Microspheres (HGMS) are near perfect spherical shapes of thin walled glass bubbles that are approximately 50 microns in size. The glass type is amorphous and can come low purity or high purity (Trelleborg) grades.
The key properties of low density HGMS are their light weight and strength. Incorporating them into buoyancy products allows Remotely Operated Vehicle (ROV), or Autonomous Underwater Vehicle (AUV) manufacturers to provide buoyancy to vehicles without the use of cumbersome pressure vessels (buoyant structures) because the material itself is buoyant (buoyant material). Some of other applications are as an alternative to conventional fillers and additives such as silica, calcium carbonate, talc, and clay in low dielectric or thermally insulating applications.
The glass bubbles can be incorporated into a wide range of polymer and resin systems and can be customized via surface treatments, material chemistry selection, density specifications, or particle size distribution, thereby being tailored to meet demanding strength, weight and electrical specifications for customers in a variety of markets.
This article comes from trelleborg edit released
Posted by admin on July 7, 2020 at 9:04 am under Hollow Glass Microspheres.
Comments Off on Applications of Hollow Glass Microspheres.
With a series of alternative materials and rapid development, especially in the application of high performance glass beads to reduce thermal conductivity and reduce deep-sea oil and gas recovery feasible.With the deep undersea oil pipeline requires the development of deeper and more to geographic location requirements increase. When depth and stressful environment, usually filled with glass beads apply foam insulation, which makes deep-sea pipeline to extend long 50km or farther underwater.
Currently the use of hollow glass microspheres filled polymer synthesis deep strong buoyancy material has been applied in foreign countries.According to reports, the current foreign developed high compressive strength, low density buoyancy material is an epoxy binder, filled with hollow glass beads and a large number of additives, such as lightweight composite buoyant material used in deep-sea submarine, in the deep seaIt can withstand high pressure, and in the basic conditions for a long time does not absorb moisture.Although China has been carried out in this field for many years of research, but in terms of diving with buoyant material properties are still lagging behind the international advanced level.
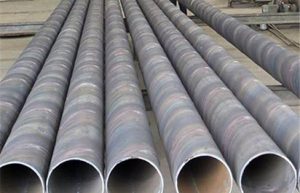
Sinosteel Maanshan Institute of Mining Research Co.,Ltd established in 1963, it belongs to one of the global top 500–Sinosteel Group.So far, we have outstandingly completed a series of major national scientific and technological tasks and 118 Science and technology support projects.Meanwhile,we complete 2 National important technological equipment localization projects, 22 state-level new products & National torch plan projects and more than 12000 projects authorized by key unit in Province and mineral enterprises. Nowadays, we have been awarded more than 500 National & provincial Prizes for Progress in Science and Technology and 102 patents.
Posted by admin on May 19, 2020 at 7:22 am under Uncategorized.
Tags: hollow glass microspheres, Sinosteel Maanshan
Comments Off on Hollow Glass Beads Applied To Deep-Sea Pipeline.